圖1 : 資誠PwC調查指出,91%的製造業公司已經在投資數位化工廠。(source:資誠PwC)
四件事加速數位轉型腳步
工業4.0希望透過數位化智慧工廠,整合生產技術、銷售、產品體驗,串連客戶、協力夥伴,創造更有價值的商業流程,以解決生產技術、經營管理模式、綠能環保需求、企業社會責任等問題。
以快時尚電商業者為例,可以靠銷售量等「客觀數據」與設計師溝通,無須因「不好看」三個字陷入無效溝通的泥淖;製造業海外設廠普遍,分散式管理難度與複雜度高,加上疫情影響,原來到處飛的老闆和員工唯有靠遠端監控等數位化方式才能克服無法到現場的難題。
數位轉型的四個管理盲點
盲點1:抓不到重點處
工業4.0不只能解決問題,還可以找出企業目標與新價值,但許多企業仍不清楚如何導入工業4.0概念,或者進入市場後刷不出存在感。資誠創新整合董事長劉鏡清指出,面對數位化浪潮,企業必須全面改變思維,從戰略大方向思考,台灣科技業與製造業習慣以技術解決問題,只有執行力沒有戰略的結果就會不知為何而戰,雖然不少龍頭產業早已擁抱數位化解決方案,實施創新技術、尋找及培養人才,但不少中小型製造業者在數位化的數位化過程中並不順利,不知因何而戰,遑論擬定戰術與策略。
盲點2:為數位化而數位化
資誠創新諮詢公司協理洪家頌指出,數位化可以產生的效益包含增加營收、降低成本、提高效率、強化客戶彈性服務,以及提高業者競爭力。不少製造業面臨缺工、勞動成本提高、效率無法提升等問題,數位化可以取代部分人力,找到低效能因素,「但不少業者錯將數位化當作執行目標,無法用出數位化真正的價值。」
舉例來說,不少業者響應「智慧機上盒(Smart Machine Box)專案,希望落實垂直整合軟體系統及硬體設備,透過M2M機聯網系統導入數位化生產,後來發現無法將投資與實際營收連結,主要就是因為執行前沒有具體目標與規劃,或者「知其然不知所以然」,沒有對應的動作呼應數位化產出的數據結果,如此自然無法體現數位化帶來的益處,這是數位轉型前沒有深思熟慮的結果。
盲點3:數位化不是萬靈丹
由於產品迭代速度變快,RD已經無法像過去一般慢慢研發,數位化可以縮短研發時間,比方模板數位化可以提高研發速度,數位化演算數據也有助改善生產流程中虛耗的成本、閒置人力或精簡流程,提高單位產值。
然而,數位化可以帶來諸多效益,卻不能解決所有問題,比方空有先進機台卻找不到人員操作,又比方中美貿易戰保護主義興起,許多大陸設廠業者遷廠到東南亞,衍生語言、文化、工作習慣差異等問題,這部分除了數位化,更需要從管理面著手。
盲點4:二代接班不易丹
台灣家族企業佔比高,面臨到的數位轉型問題不太一樣,比方第一代創業者對新事物接受度較低,不靠數位化與自動化就能打下江山的他們,難以體會數位轉型或導入數位化工具的必要性,加上導入數位化投資成本不低,就算二代接班人對數位化接受度高,導入過程中同樣需要面對公司內部新舊世代成員因價值觀不同而產生的溝通成本,不了了之或虎頭蛇尾的案例不少。
雖然數位化過程遭遇不少難題,洪家頌仍看好台灣製造業未來的成長性,主要因為亞洲代工多,有來自客戶與競爭對手的要求與壓力,所以數位化成長速度快,尤其品牌端特別需要數位化提供的數據資料用來改善、說服客戶與自身團隊,這些因素有助加速數位化轉型。
除了「護國神山」級的製造業龍頭或領導品牌因為擁有豐沛資源可以大力推動數位化,以中小企業居多的台灣製造業多半擁有技術優勢,數位化轉型的進步空間很大,爆發力強,但缺點是管理較為鬆散,「若能導入數位化工具搭配管理優化,調整管理思維,可以帶來很好的數位轉型結果。」
數位轉型的六個管理思維
思維1:不為數位化而數位化
洪家頌強調,許多業者無法順利數位化轉型主要是因為他們陷入「為數位化而數位化」的迷思,或者將數位化當作目標而非工具。資誠(PwC)調查指出,數位化工廠約需2-5年才可能回收,91%的製造業已經投資數位化工廠,卻只有6%受訪者認為達到「完全數位化」,不少企業主事者將數位化錯當成目標而非達成目標的工具,也是投入數位轉型後看不到明顯成效的原因之一,很多公司執行數位化的過程比較像是建置Show Room,客戶參觀時開放,沒人看了就閒置,當然無法收效。

曾有一家規模800億元的電子製造業投資工業4.0兩年卻看不到明顯進展,開會報告總是圍繞「自動化」走,卻看不到數位化實際成果,就是因為公司錯將工業4.0當作目標而非工具。除了硬體的數位化更新,數位轉型還要搭配管理手法,如縮短流程、溝通與時間等隱形成本,讓流程透明化、數據化,當生產過程可以量化,部門間的協作及溝通速度就會變快。
思維2:建立並強化戰情室功能
數位化的管理概念好比機場的控制塔台,由中控中心負責調度、擬定執行方案(action plan)並追蹤成效,落實於製造業工廠內部,還要納入工業、物業、生管、規劃、採購等相關人員,不是單純地投資數位化硬體設備就可以坐等數位轉型發揮作用。中控中心好比戰情室,如果戰情室看到產能在某個小時下降2%,會下達action plan,限時、限管理層級解決問題,如果沒有如期解決問題再拉高層級,過去業者只有監看數據與生產流程,現在則要提出解決方案與執行方法,才會因改變而產生成效。
思維3:一次一小步,目標要明確
除了不為數位化而數位化,洪家頌還建議在數位轉型的過程中,先設定小目標,不求一步到位。想做數位轉型的企業有兩種,一種是看到其他企業的數位化成效起而效尤,希望強化自己的競爭力,另一種是退無可退,要求生存,不論動機為何,投資數位轉型如果可以在一季內看到成效,企業更願意繼續嘗試改變,「第一次執行數位化轉型,時間太長容易疲乏,要讓所有人有參與感、認同感,一步一步證明數位化對公司的真正價值,先抓小成功,有成果後才能產生續航力。」
思維4:全方位思考,點線面一手抓
《工業4.0:即將來襲的第四次工業革命》作者桑德勒(Ulrich Sendler)表示,工業4.0的定義是整個系統或價值鏈的全生命週期管理與服務(SysLM),從顧客服務驅動研發、供應鏈和生產流程。因此,工業4.0不是單純地升級機器或電腦等硬體設備,還包含掌控許多協作溝通等隱形成本,比方與內部、跨部門員工溝通,與供應商、客戶溝通,不能單看點、線、面,要全方位、多方思考,否則容易流於表面。
洪家頌指出,思考面向及執行複雜度視產業特性而異,有些企業只要自己數位轉型就可以應付未來3-5年競爭,有些要想辦法往供應鏈等方向延伸,甚至將競爭對手的威脅納入考量,「越靠近品牌端要跟得越快,反之,越傳統的製造業改變速度就比較慢,因為不在核心,改變壓力也小。」最明顯的例子就是蘋果(Apple)供應鏈,「如果競爭對手有新的技術或投入數位轉型而我沒有,無法向客戶證明自己有能力成為供應商。
思維5:敏捷式管理,善用KPI+OKR
數位轉型的管理思維不妨善用敏捷式(Agile)作法,領導者不只自己要敏捷起來領導團隊,還要授權跨部門協作,強化員工投入改變的「誘因」,才能製造團隊「推力」,留住人才,甚至扭轉組織文化。此外,組織成員要願意擁抱改變,樂於分享,才能逐步由小團隊擴大影響力到跨部門、跨國際團隊,甚至帶動上下游合作夥伴、客戶改善協作方式,必要時可以透過外部力量,協助公司快速找到盲點與方向,「規劃的目標是願景(藍圖),要找到競爭核心,再用數位化工具達成目標。」洪家頌提醒,除了用關鍵績效指標(Key Performance Indicator, KPI)評估轉型「績效」,更要懂得善用目標和關鍵成果(Objectives and Key Results, OKR)以確認轉型「方向」無誤,以免失焦導致資源浪費。
思維6:解決問題與發現問題一樣重要
許多製造業面臨產能不足的窘境,機台陷入產能爆炸,所以買機器、擴廠增員,但其實問題可能不在機器,用一顆sensor就能找出原因。Sensor觀察到,白天機台真正運作的時間只有40%,換線、上下料、檢查、調整機器參數等時間卻高達60%,想衝產能的晚班效能更糟,後來調整將上下料工作交給自動化、檢查工作交給主機手之外的其他人做,便大幅提高效能,根本無須擴廠增員。洪家頌指出,很多問題出在人,數位化可以更客觀地找出原因,之後針對原因找適合的解決方案即可,「發現問題是簡單的,解決問題卻不簡單,需要搭配自動化、品檢標準化等管理面措施,未來還可以善用AI數位化改善問題。」
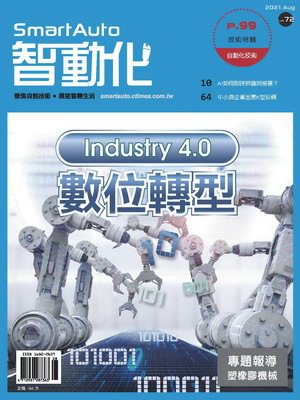
※欲閱讀更豐富的內容及更多精彩報導,詳見《智動化SmartAuto》網站